I have wanted to cover the plastic hatchback panel, ever since I upgraded to leather Flofit seats. I made sure that Seat Source sent me all of the extra leather (almost a complete hide!!) just so that I would have it for such projects and repairs etc. Well, after 3 years, I finally decided to cover the plastic panel, with red leather, matching my seats. This will also add a nice tie in, adding the red burgundy color, to the porno red hatch areas.
I also thought that it would be cool, to add the SALEEN logo, to this panel, kind of like Saleen did, with the 1999-2004 cars, with their logo'd trunk panel. I purchased a black street sign, with silver Saleen logo, planning on 'frenching' it in, to this panel. However, the street sign proved to be too small, and honestly, it would look just plain cheesy, really cheap looking. So I decided to try my hand at the upholstery technique of embossing the logo, in foam, then covering the panel. Similar to what you see on hot rods, with flames embedded into the door panels etc. So I used the street sign, for a template, and simply scaled up the SALEEN letters, to better fit the panel. Here is the panel, with the paper templates. And no, I didn't forget how to spell Saleen, I only made one 'E' template, which I will duplicate!!
Next I transferred the paper templates on to cardboard, and then finally on to foam. I had a hard time, finding the foam, as I was impatient, and didn't want to order off of the internet and wait for shipping. I found this 3/16" foam, made for laying on metal shelving. You know the kind of closet shelving, made of wire? This lays on it, providing a nice flat surface, so your clothes don't get wire dents in them, or so your cans of food will lay flat, in your pantry, etc. I watched a couple of tutorials, on Youtube, and they all recommended using a razor blade, to cut the foam. I found that this really did work better, than scissors, as you can cut the foam, on a 45 degree bias, providing a much cleaner, more distinct edge. I also used high quality 3M spray adhesive, to attach the foam letters, to the Mustang panel. It worked, really well, but did not leave a lot of time, to move the letters around. I was confident, in my placement, and had the letters/template well layed out, with plenty of witness marks! Here is the panel with the foam letters, glued on, and a close up of the 'S' profile.
Thats it, for now, I will be gluing on the leather, in the next day or so, so stay tuned for an update! BTW, if anyone has any experience with steaming creases/folds out of leather, please chime in. I was planning on using my Steam Shark, to get the leather to lay perfectly flat?
Anyway, here is an updated pic:
I adhered the leather to the panel, today. I set up a little work bench, out in the sun, and let the leather get nice and warm, first. I started from the center, gluing just the letters, and working my way out to the sides. Like all of my projects, it is not perfect! However, I am OK with that, I have learned to accept, just a shade away from perfection, over the years, lol! A couple of the letters, the edges aren't as sharp or as crisp as I would have liked, but I did end up with no bubbles or wrinkles! I am planning on letting the panel sit, for another day or two, just a few hours each, in the sun. It is my experience, that the leather will contract and shrink, and actually end up looking better. I have used the spray adhesive before, and in the past the media, that was glued, actually shrunk, quite nicely. We'll see. Final pic will be of the panel, mounted up in the hatch of my car.
Not mounted in the car, yet. I will probably get it done, over the weekend. I did take a better pic, of the panel, basking in the sun, earlier today! I had to remove a screen, and lean out a window, to get this pic! The panel is rather large, and it is nearly impossible to get the whole thing into frame, for taking a digital pic. Anyway, I let it sit in the sun, for a while, then went over the whole thing with a decal squeegee. It actually got rid of a couple of bubbles, that had developed overnight, and helped to sharpen up the letters' edges. I felt that too much sun, would be a bad thing, and cause the glue to get soft, and release. So I left it out, for just a little while, then back into the basement, to cool.
BTW, if anyone else wanted one, I would be happy to make one for you! I would just need you to send me your panel, and whatever cloth or leather etc. that you wanted it covered with. I think that shipping back and forth, would be cost prohibitive, however. If anyone was interested in just a set of the foam letters, for a DIY project, just let me know, I would be happy to send any club member a set, you pay for shipping, only!
As promised, here are the pics of the finished product! Once again, I am absolutely thrilled, with how this project turned out.
Anxious to hear your feedback!
Thursday, August 9, 2012
Labels:
1989 Mustang,
3M,
custom,
Fox,
GT,
interior,
leather,
porno red,
Saleen,
spray adhesive
Like a lot of you guys, I have way too many powered accessories! Which, of course, includes a bunch of power wires, cluttering up my engine bay and/or fuse panel. For example, I have: one wire for the alarm, one for my Ipod controller, one for my power amp/subwoofer, one for my external T-Rex fuel pump, and finally one for my Crane ignition box!! That is too many wires, with three directly on my battery, and two on the starter solenoid. It looked like crap, to put it plainly. It needed to be cleaned up, and with my 1st show approaching, now was the time.
So I began my search looking for a power distribution block. Sounds easier than it was. Believe it or not, there is not that much out there! There is plenty of stuff for the bling crowd, mostly car audio related. All of these products have flashy colors, lots of clear plastic, gold plated terminals, blah blah blah. Nothing that I would put under the hood of my now 20 year old Stang. Luckily, I discover Wiringproducts.com. They have a few decent, well-made products, mostly finished in black and stainless steel. I also learned the difference between a power junction block, and a power distribution block. The junction is useless for distributing power, it is, as the name states, used for only a 'junction' or single connection. Luckily, that lesson only cost me $50 worth of wrong parts, that I can still return! lol
So I ended up with this:
Here is the link: http://www.wiringproducts.com/index1.html
Next I fabbed up a nice large gauge cable. I did use the blingy type of audio cable, simply because I had some on hand, and it was going to be hidden, in the fender well, for the most part. I used heavy duty copper terminals, soldered in place, with a torch. I also used a really good quality glue infused heat shrink tubing. I want this setup to last, function well, and be indestructable! Here is the cable:
Originally, I wanted to mount my block, behind the battery, up against the fender, as there is actually a good deal of room there. However, the distribution block I ended up using would not fit. It is kind of bulky, and features a large 3/8" stud. You could even wire one of those single wire alternators to this thing if you were so inclined. I neatly tucked the large gauge wire, in the fender well, routing it through the washer fill opening, and one of the many 'swiss cheese' holes in the fender. That part was easy.
In all of my 'messing around' in the area behind my battery, I broke off one of the plastic tabs, holding my washer fluid reservoir in place! Never fails, a 'simple' project just keeps getting more and more complicated! The damn thing is full, and heavy, and I haven't used it since I bought the car! (that was when I foolishly filled it, to the brim) Next car wash I will be judiciously dumping most of that fluid! I was able to fix it with an industrial width/length zip tie of sorts. My friend gets these for free, they are used by the power companies to hold overhead electrical lines in place, so needless to say, they are tough! There are plenty of holes and slots to route the tie, but I did have to lift the car and attack it, from below, to thread the damn thing through! As I hoped, the fix cannot be seen, and it should last a good bit longer than Ford's inferior mounting system! I also found that before the mounting tab broke, the tank was sagging, due to the weight, and the rubber hose was rubbing on the horn mounting bracket. If I didn't plan on emptying this thing, it would have emptied itself at some point! If you don't use your windshield washer, I highly recommend emptying that reservoir! It is not mounted very well, and if it left full, over time, the plastic tabs will break -- you have been warned!
Anyway, I found another spot, bolted to the radiator header panel, in front of the battery, towards the front of the car. This necessititated lengthening all of my power wires, save one, which was a major PITA, considering that all of my cables were hidden in split loom, heat shrunk etc. etc! Here is where it ended up:
Note the desired end product, of nothing wired up to the battery, except for the positive and negative cables, as it should be. Although it can't be seen, due to the coil cover, there is nothing 'extra' cluttering up my solenoid, either.
And a close up pic:
I used on of those red boots off of a one wire alternator, just to insulate the connection. It was not necessary, but I tend to incorporate a lot of overkill in my projects! I tested it out, and so far so good, everything powered up just fine!
ps. The battery is a custom made, high powered Interstate battery. Interstate dealers generally don't stock the MTP (high power) 58 series, for some reason. They all have 58R's with reverse terminals, though?! Strange. Anyway, the custom order didn't cost any more, and it comes through finished in plain black. A couple of eBay Champion stickers later, and it really complements the look, underhood, with the ties to Champion being the original battery supplier to Saleen.
So I began my search looking for a power distribution block. Sounds easier than it was. Believe it or not, there is not that much out there! There is plenty of stuff for the bling crowd, mostly car audio related. All of these products have flashy colors, lots of clear plastic, gold plated terminals, blah blah blah. Nothing that I would put under the hood of my now 20 year old Stang. Luckily, I discover Wiringproducts.com. They have a few decent, well-made products, mostly finished in black and stainless steel. I also learned the difference between a power junction block, and a power distribution block. The junction is useless for distributing power, it is, as the name states, used for only a 'junction' or single connection. Luckily, that lesson only cost me $50 worth of wrong parts, that I can still return! lol
So I ended up with this:
Here is the link: http://www.wiringproducts.com/index1.html
Next I fabbed up a nice large gauge cable. I did use the blingy type of audio cable, simply because I had some on hand, and it was going to be hidden, in the fender well, for the most part. I used heavy duty copper terminals, soldered in place, with a torch. I also used a really good quality glue infused heat shrink tubing. I want this setup to last, function well, and be indestructable! Here is the cable:
In all of my 'messing around' in the area behind my battery, I broke off one of the plastic tabs, holding my washer fluid reservoir in place! Never fails, a 'simple' project just keeps getting more and more complicated! The damn thing is full, and heavy, and I haven't used it since I bought the car! (that was when I foolishly filled it, to the brim) Next car wash I will be judiciously dumping most of that fluid! I was able to fix it with an industrial width/length zip tie of sorts. My friend gets these for free, they are used by the power companies to hold overhead electrical lines in place, so needless to say, they are tough! There are plenty of holes and slots to route the tie, but I did have to lift the car and attack it, from below, to thread the damn thing through! As I hoped, the fix cannot be seen, and it should last a good bit longer than Ford's inferior mounting system! I also found that before the mounting tab broke, the tank was sagging, due to the weight, and the rubber hose was rubbing on the horn mounting bracket. If I didn't plan on emptying this thing, it would have emptied itself at some point! If you don't use your windshield washer, I highly recommend emptying that reservoir! It is not mounted very well, and if it left full, over time, the plastic tabs will break -- you have been warned!
Anyway, I found another spot, bolted to the radiator header panel, in front of the battery, towards the front of the car. This necessititated lengthening all of my power wires, save one, which was a major PITA, considering that all of my cables were hidden in split loom, heat shrunk etc. etc! Here is where it ended up:
Note the desired end product, of nothing wired up to the battery, except for the positive and negative cables, as it should be. Although it can't be seen, due to the coil cover, there is nothing 'extra' cluttering up my solenoid, either.
And a close up pic:
I used on of those red boots off of a one wire alternator, just to insulate the connection. It was not necessary, but I tend to incorporate a lot of overkill in my projects! I tested it out, and so far so good, everything powered up just fine!
ps. The battery is a custom made, high powered Interstate battery. Interstate dealers generally don't stock the MTP (high power) 58 series, for some reason. They all have 58R's with reverse terminals, though?! Strange. Anyway, the custom order didn't cost any more, and it comes through finished in plain black. A couple of eBay Champion stickers later, and it really complements the look, underhood, with the ties to Champion being the original battery supplier to Saleen.
Labels:
1989 Mustang,
accessories,
battery,
Champion,
Fox,
GT,
power junction,
Saleen,
wiring
1989 Ninja ZX7 Header Wrap
In an effort to keep this section from becoming a desolate wasteland, (I keep looking for tumbleweeds to blow by around here, lol!) here are some pics of one of my minor winter projects. I had an old gift certificate from Summit Racing, that was burning a hole in my pocket. In addition to my Mustang, I also have a really nice, perfect shape 1989 Kawasaki Ninja ZX7. No big surprise, as most car guys are into motorcycles, as well. Somebody over on the ZX Forums posted up a nice thread about wrapping his headers with exhaust wrap. He also has a nice set of full stainless Muzzy exhaust, which is what I run. Only mods to my bike are the aforementioned exhaust, K&N filter and a very minor jet upgrade to accomodate the exhaust and air filter, thats it. Anyway, no how to or step by step pics, just the finished pics of the finished product, right after I finished painting the wrapped headers with the high temp silicon paint. I got a complete DEI kit, from Summit, with enough wrap and stainless steel ties to do a standard set of V8 headers, more than I needed. I'm sure that some of you guys have done this, before. It is a tedious process, that takes a lot of patience. It is also messy, as there is a lot of 'gunk' in the wrap, that comes out, when you wet it. In addition, as you can see, my headers are actually quite close together, with a couple of the bends, so it was challenging, pulling them apart and feeding the limp noodle wet exhaust wrap through the crack!! Enough rambling, here are the pics;
I was also able to get the header mounted back up, despite extreme cold temperatures, and being too stubborn to remove the radiator! A couple of scraped knuckles later, it was definitely worth it. Finally a couple of pics of the bike:
I forgot to mention, I'm really hoping that the exhaust wrap helps to tame the high running temps that these bikes are notorious for. With the headers being sandwhiched between the heads and the radiator, I'm sure that the extreme radiant heat, wasn't helping the cause. The wrap is supposed to be super efficient, in keeping the heat, within the header, and right out of the tailpipe. We'll see. I also am hoping for some limiting of the tinny, buzziness of the exhaust. I also repacked the Muzzy can, and added an additional baffle. I'm not expecting miracles, but I'm sure that even these small changes will make a difference. Its either that, or I start to wear earplugs, under my helmet! I must be getting old...
I was also able to get the header mounted back up, despite extreme cold temperatures, and being too stubborn to remove the radiator! A couple of scraped knuckles later, it was definitely worth it. Finally a couple of pics of the bike:
I forgot to mention, I'm really hoping that the exhaust wrap helps to tame the high running temps that these bikes are notorious for. With the headers being sandwhiched between the heads and the radiator, I'm sure that the extreme radiant heat, wasn't helping the cause. The wrap is supposed to be super efficient, in keeping the heat, within the header, and right out of the tailpipe. We'll see. I also am hoping for some limiting of the tinny, buzziness of the exhaust. I also repacked the Muzzy can, and added an additional baffle. I'm not expecting miracles, but I'm sure that even these small changes will make a difference. Its either that, or I start to wear earplugs, under my helmet! I must be getting old...
Wednesday, August 8, 2012
I just took apart my sport panniers, in preparation to paint them. It was a bit 'fiddly' figuring out how they come apart, but overall it was quite simple. Here are the steps:
1. Inside of the case there are two small torx bolts that appear to be holding the lid string stays in place. Remove both of these, they have nothing to do with the strings, and they actually hold the black plastic case protectors in place. Take care with the small parts, as there is also a metal insert, in the lid that the bolt goes through, that will be loose.
2. Once the bolts are removed, the black plastic case protector can be swung out of the way, exposing the inner hinge. There are four phillips screws in the inner hinge crevice, remove them. On the left pannier all 4 are located in the hinge cavity. On the right hand pannier, three are in the hinge area, one smaller screw is inside the case. Unsnap the string stays from the inner case, now the entire lid and the black plastic protectors can be removed as an assembly.
3. The black case protectors can be separated from the lid by separating the two hinges. The grey lids hinge is just a portion of the metal rod that the lid uses for strength. It takes a little bit of manipulation to separate the rod from the black case protector hinge, but once they are apart, you are done.
Here is a pic of the case protectors, swung out of the way, once the top/lid portion of the panniers has been removed:
Now you have just the grey lid portion, ready for painting. The expandable vinyl portion does not appear to come off, and looks to be sewn on. This will have to be masked off, unless you plan on painting it as well (with vinyl dye or similar).
I am going to use a black satin plastic fusion paint on mine. I am undecided as to whether or not I am going to dye the vinyl expansion portion black or not, so I am looking for opinions? Thanks.
I painted mine up today. The weather was beautiful, around 70 degrees with no humidity. I took my sport panniers apart, and masked them off. Then I cleaned and degreased them. I gave them a light scuff with a red Scotch Brite pad, even though the surface is quite textured, already. Then I cleaned them again and again and again. I used Duplicolor adhesion promotor then Duplicolor flat black acrylic enamel. Multiple light coats of each. The paint job came out, fantastically, if I do say so myself! I haven't decided if I am going to use black vinyl dye on the grey expandable portion of the panniers. I do not intend to run the panniers, in their expanded position, ever, so I may just leave it, as a slight contrast. We'll see once I get them put back together. This project was very easy, and I would recommend it to anyone, with even the most basic DIY skills!
I snapped a couple of pics:
ps. The 'Do Not Touch' is for my kids, from a previous project, left drying in their line of fire, lol!
I am still torn on whether or not to use the black vinyl dye on the expandable grey vinyl portion. I definitely do not like the contrasted look, from the flat black case, to the grey/silver liner. However, they will not show, when the cases are closed up. Lastly, now is the time, if I want to dye the vinyl black, while the cases are all torn down. I also have to wait for good weather! Although yesterday was beautiful, rain is forecast for the rest of the week. :( I'm certain that the vinyl will accept the dye, very well, and most likely that is the route that I am going to go with. Here are a couple of pics of the case tops, with the masking removed:
I got the expandable grey vinyl painted up today. The weather wasn't quite as nice as I would have liked, as it was only 60 degrees. However, I put the cases in the direct sun for a while, and the new black paint heated up quite nicely. The Duplicolor vinyl and fabric dye is very easy to use, and also very forgiving. The dye is super thin, as it is designed to sink into and penetrate the vinyl, as it is a dye, not a paint. It will run, so multiple thin coats is the way to go. You have to make sure that you are starting with a very clean surface to dye, as well. I know the pictures are grainy, but the final product looks great! Here are a few pics:
The next installment will be a 'prequel' with pics of the assembly, in reverse, added to the post, describing how to take apart the panniers. This thread, when completed could be moved to the 'How To' section, as there is precious little out there about our high tech expensive panniers.
Here are a couple of 'top tips' for re-assembly; the cases [u]must[/u] be re-assembled in this order! Refer to the disassembly pics, for reference!
1. Screw the exterior case protector to the bottom of the back half of the case. Only re-install the two outer screws at this time! The two inside screws need to be left off, so that the case lid will still easily snap back into place. The two inner screws hold tension against the plastic tab that holds the hinge in place. (I removed the two inner screws, once I figured this out, lol!)
2. Now manipulate the metal rod/hinge on the cover into place, snapping it into the plastic side of the hinge, on the backside of the case.
3. Re-install the two center phillips head screws on the hinge panel. A right angle phillips head or phillips head socket makes this step easier, just take care not to strip out the screw heads, as they are now obstructed by the case top/lid.
4. Re-install the two t-15 torx bolts/spacer/washer assembly on the inside of the case, which hold the exterior case protector in place. Some pressure may need to be applied to the case protectors, to get the holes to line up.
5. Snap the string stays back into place and you are done!
And the final product:
Definitely interested in feedback, and success stories, if anyone else out there does this!
1. Inside of the case there are two small torx bolts that appear to be holding the lid string stays in place. Remove both of these, they have nothing to do with the strings, and they actually hold the black plastic case protectors in place. Take care with the small parts, as there is also a metal insert, in the lid that the bolt goes through, that will be loose.
2. Once the bolts are removed, the black plastic case protector can be swung out of the way, exposing the inner hinge. There are four phillips screws in the inner hinge crevice, remove them. On the left pannier all 4 are located in the hinge cavity. On the right hand pannier, three are in the hinge area, one smaller screw is inside the case. Unsnap the string stays from the inner case, now the entire lid and the black plastic protectors can be removed as an assembly.
3. The black case protectors can be separated from the lid by separating the two hinges. The grey lids hinge is just a portion of the metal rod that the lid uses for strength. It takes a little bit of manipulation to separate the rod from the black case protector hinge, but once they are apart, you are done.
Here is a pic of the case protectors, swung out of the way, once the top/lid portion of the panniers has been removed:
Now you have just the grey lid portion, ready for painting. The expandable vinyl portion does not appear to come off, and looks to be sewn on. This will have to be masked off, unless you plan on painting it as well (with vinyl dye or similar).
I am going to use a black satin plastic fusion paint on mine. I am undecided as to whether or not I am going to dye the vinyl expansion portion black or not, so I am looking for opinions? Thanks.
I painted mine up today. The weather was beautiful, around 70 degrees with no humidity. I took my sport panniers apart, and masked them off. Then I cleaned and degreased them. I gave them a light scuff with a red Scotch Brite pad, even though the surface is quite textured, already. Then I cleaned them again and again and again. I used Duplicolor adhesion promotor then Duplicolor flat black acrylic enamel. Multiple light coats of each. The paint job came out, fantastically, if I do say so myself! I haven't decided if I am going to use black vinyl dye on the grey expandable portion of the panniers. I do not intend to run the panniers, in their expanded position, ever, so I may just leave it, as a slight contrast. We'll see once I get them put back together. This project was very easy, and I would recommend it to anyone, with even the most basic DIY skills!
I snapped a couple of pics:
ps. The 'Do Not Touch' is for my kids, from a previous project, left drying in their line of fire, lol!
I am still torn on whether or not to use the black vinyl dye on the expandable grey vinyl portion. I definitely do not like the contrasted look, from the flat black case, to the grey/silver liner. However, they will not show, when the cases are closed up. Lastly, now is the time, if I want to dye the vinyl black, while the cases are all torn down. I also have to wait for good weather! Although yesterday was beautiful, rain is forecast for the rest of the week. :( I'm certain that the vinyl will accept the dye, very well, and most likely that is the route that I am going to go with. Here are a couple of pics of the case tops, with the masking removed:
I got the expandable grey vinyl painted up today. The weather wasn't quite as nice as I would have liked, as it was only 60 degrees. However, I put the cases in the direct sun for a while, and the new black paint heated up quite nicely. The Duplicolor vinyl and fabric dye is very easy to use, and also very forgiving. The dye is super thin, as it is designed to sink into and penetrate the vinyl, as it is a dye, not a paint. It will run, so multiple thin coats is the way to go. You have to make sure that you are starting with a very clean surface to dye, as well. I know the pictures are grainy, but the final product looks great! Here are a few pics:
The next installment will be a 'prequel' with pics of the assembly, in reverse, added to the post, describing how to take apart the panniers. This thread, when completed could be moved to the 'How To' section, as there is precious little out there about our high tech expensive panniers.
Here are a couple of 'top tips' for re-assembly; the cases [u]must[/u] be re-assembled in this order! Refer to the disassembly pics, for reference!
1. Screw the exterior case protector to the bottom of the back half of the case. Only re-install the two outer screws at this time! The two inside screws need to be left off, so that the case lid will still easily snap back into place. The two inner screws hold tension against the plastic tab that holds the hinge in place. (I removed the two inner screws, once I figured this out, lol!)
2. Now manipulate the metal rod/hinge on the cover into place, snapping it into the plastic side of the hinge, on the backside of the case.
3. Re-install the two center phillips head screws on the hinge panel. A right angle phillips head or phillips head socket makes this step easier, just take care not to strip out the screw heads, as they are now obstructed by the case top/lid.
4. Re-install the two t-15 torx bolts/spacer/washer assembly on the inside of the case, which hold the exterior case protector in place. Some pressure may need to be applied to the case protectors, to get the holes to line up.
5. Snap the string stays back into place and you are done!
And the final product:
Definitely interested in feedback, and success stories, if anyone else out there does this!
Chicane Gauge Cage Install
If any of you have been following the vent/pillar gauge thread in the Open Discussion forum, then you know that I recently purchased the Chicane gauge cage panel. It was expensive at $149, versus $40 bucks for the Autometer product. After a lengthy conversation with Joe Gosinksi, owner/fabricator of Chicane Sports Tuning, my choice was clear. Joe worked at Saleen for 10+ years, and designed a lot of products during his tenure there. The Fox era pedal covers, the S351 double pass radiator and the Saleen race gauge panel, were all designed and built by Joe. The original gauge panel was put in to Tim Allen's RRR (Casper) car. Then the panel went into supercharged SC's and the SA-10's. Autometer approached Saleen, about producing their own gauge panel, and Saleen (the man) turned them down flat. Unfortunately, the part was not patented, and Autometer went ahead and manufactured their own product, anyway. Saleen complained, to no avail. The Autometer product is not the same, not even close. They made quite a few changes, for ease of manufacture, and pricing, none of them for the better!
After speaking with Joe Goskinski, and Mark LaMaskin, I came up with this interesting tidbit. Saleen put the gauge cage into a few of their production cars. A very small number, of the original, handmade pieces, were sold through the Speedlab. After Saleen could not or would no longer manufacture the handmade piece, they actually began to sell the Autometer part, through the Speedlab!! Those in the know, will not be surprised, by this questionable move, by Saleen. What the hell, the Autometer part was readily available, and cheap, at 1/3 the price of the handmade piece. So Saleen could still sell the Autometer plate, and two inexpensive Made in Mexico VDO gauges, for $299!! (FP isolators $100 extra!!)
Here is why. Check out the profile of the Autometer panel. It is very thin, and flat. Also note the thin piece of sheet metal, used to hold in the modified AC vents.
Now the Chicane part. Notice that it is very thick, easily more than twice as thick as the Autometer part. It is also curved, to match the curve in the dash pad. The tabs that hold in the AC vents are welded in place, making one solid piece. The Chicane piece is also powdercoated, a flat, brushed black.

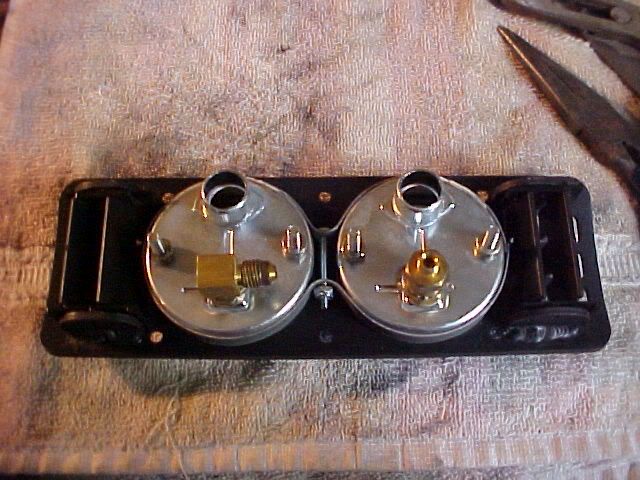
Anyway, I get the whole shebang re-installed, with the new backing plate, and it tightens up, beautifully, matching the curve of the dash pad. Here is a pic of the finished product:
And at night:
I used those slick little Autometer 'hats' that go over the light bulbs, to change their color. Green in my case to match the factory dash.
This should in no way, be viewed as a criticism, other than constructive, of the Chicane product. It is a 100% handmade custom piece. These minor problems are to be expected when dealing with something that is custom made. If you want easy, then stay away from the custom stuff! This is what makes our hobby fun, the sanding, and grinding, and modifying things to fit!! The end result is well worth it!
After speaking with Joe Goskinski, and Mark LaMaskin, I came up with this interesting tidbit. Saleen put the gauge cage into a few of their production cars. A very small number, of the original, handmade pieces, were sold through the Speedlab. After Saleen could not or would no longer manufacture the handmade piece, they actually began to sell the Autometer part, through the Speedlab!! Those in the know, will not be surprised, by this questionable move, by Saleen. What the hell, the Autometer part was readily available, and cheap, at 1/3 the price of the handmade piece. So Saleen could still sell the Autometer plate, and two inexpensive Made in Mexico VDO gauges, for $299!! (FP isolators $100 extra!!)
Here is what I started with. Note that the Autometer plate is completely flat, and does not fit well, at all. The dash pad is curved!! Also the corners are bent up, when the screws are tightened etc.
Here is why. Check out the profile of the Autometer panel. It is very thin, and flat. Also note the thin piece of sheet metal, used to hold in the modified AC vents.
Now the Chicane part. Notice that it is very thick, easily more than twice as thick as the Autometer part. It is also curved, to match the curve in the dash pad. The tabs that hold in the AC vents are welded in place, making one solid piece. The Chicane piece is also powdercoated, a flat, brushed black.
Now check out the backing plates. The Autometer (left) and the Chicane (right) Notice how their is a large area for the AC to flow through the Chicane piece. Also notice that the threaded inserts are pressed/riveted in, from the front, on the Chicane piece, (more on that later). Also, the Autometer plate is much thinner, of course.
So I go to drop my gauges in, and they don't fit!! WTF! So I try my old Ford Racing gauges, and they don't fit, either! I guess the powdercoating and the handmade tolerances, have left the openings a tiny bit too small, for the gauges. So out come the files and sandpaper, to open up the holes. I could have used a dremel, or a small sanding drum, but I wanted to remove as little material as possible, for a nice, tight fit. Also, the Chicane piece includes two curved trim rings, so that the flat gauges will mate up to the curved panel. They are billet aluminum, and anodized black, very, very trick, indeed! However, this means, that you have one shot, to get the gauges in straight, and line up the trim rings, with the plate. Otherwise, you are pulling it apart, and scratching everything up -- unacceptable. I did pretty good, with one shot, I scored about a 98%, but i am overly critical of myself, nobody else would ever notice the difference! Here is where we are now:

And from the back:
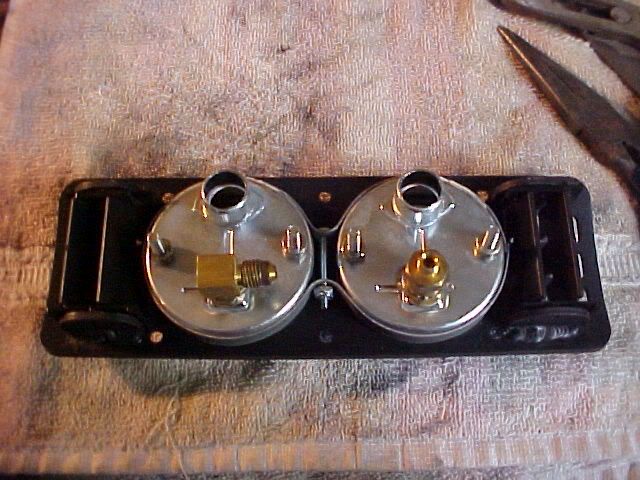
So I get everything hooked up, electrical connections, vacuum line, isolator hose etc, and the Chicane backing panel slid into place, ready for final assembly. I finally get all 6 allen screws started, and if you have ever done this, 6 blind little screws is a major PITA. Then you just tighten up the plates, sandwiching the dash pad. Chicane includes very nice button cap allen screws, versus the autometer which has large diameter regular allen screw heads (ugly) So I set about tightening up the panel, kind of like torque-ing head bolts, a little at a time. I go to finally tighten the last screw, and I hear a metallic 'POP' from behind the assembly. One of the screws is now free, and no longer threaded into the backing plate. Yep, one of the pressed in/riveted thread inserts has popped right out of the Chicane piece!! I string together enough curse words to make George Gast (sailor) run for cover, and resign myself, that I will be starting over. All screws have to come out, and all connections undone to get the backing panel removed. One of the threaded inserts was placed too close to the edge, and there was not enough material to support it, and the plate cracked. If I had any foresight, I would have simply turned the backing panel around, so that the inserts would be less likely to pull out. Oh well, I simply installed it the way it was shipped to me, pre-assembled. If you buy the Chicane panel - You have been warned!! ](*,)
Luckily, I have two Autometer backing plates, to serve as backup. One of them is a very early piece, that actually came from the Speedlab. It is thick, and the threads are welded in, from behind the backing panel. However the vented area is much smaller, restricting the AC flow. So I get out the hacksaws and a large file, and go to town, enlarging the vents. Add another 1/2 hour to the project, lol! I also previously matched up the Autometer plate, to the Chicane, and the scew holes line up, and they are the same diameter, thank God!! Here is a pic, just before the 'carnage.'
Luckily, I have two Autometer backing plates, to serve as backup. One of them is a very early piece, that actually came from the Speedlab. It is thick, and the threads are welded in, from behind the backing panel. However the vented area is much smaller, restricting the AC flow. So I get out the hacksaws and a large file, and go to town, enlarging the vents. Add another 1/2 hour to the project, lol! I also previously matched up the Autometer plate, to the Chicane, and the scew holes line up, and they are the same diameter, thank God!! Here is a pic, just before the 'carnage.'
And at night:
I used those slick little Autometer 'hats' that go over the light bulbs, to change their color. Green in my case to match the factory dash.
This should in no way, be viewed as a criticism, other than constructive, of the Chicane product. It is a 100% handmade custom piece. These minor problems are to be expected when dealing with something that is custom made. If you want easy, then stay away from the custom stuff! This is what makes our hobby fun, the sanding, and grinding, and modifying things to fit!! The end result is well worth it!
Driveshaft Safety Loop Installation
I have been looking into doing some local hillclimbs with my Mustang, and one of the requirements, that I don't have, is a driveshaft safety loop. If I ever intended to drag race, a safety loop is also required, once you go under 14 seconds! lol. You don't want to end up pole vaulting your car like this guy:
http://www.youtube.com/watch?v=k9DVlnX0jIc
So I chose the Ford Racing loop, made by HPM. The products that Ford Racing puts their name on, in my experience, are well built and also fit very well. The FRRP loop is also specifically designed, to clear the FRRP oversized aluminum driveshaft, which I am running. Unfortunately, the part is now discontinued, and I had links to Jeg's and Steeda, to purchase it, that are now dead. Luckily, I found that Brothers Performance had 1 (!) left, so I ordered it up. Here is how it is 'supposed' to come:
Mine came with only 4 nuts/bolts to hold the loop brace to the cross brace, none of the bolts to mount the assembly to the car!? I called Brothers Perf. and they said that I got the last one, there was no way they could even verify that it was supposed to come with the other nuts/bolts/washers etc. Honestly, I was just looking for a partial refund, or maybe some in-store credit? Anyway, I got nothing, other than a "sorry, I guess you'll have to go to the hardware store." Oh well, previously I have had excellent experiences with Brothers, so really no big deal. I had always intended to replace the included hardware with grade 8 bolts/washers, anyway, but the 12 grade 8 - 5/16" bolts/washers and stop nuts cost me an extra $10. DS safety loop was $50 shipping included, BTW. For those who still need one, Summit sells an exact copy of the FRRP product, with the only difference being theirs is powdercoated black, the FRRP is zinc coated. I painted mine with self-etching primer and gloss black Duplicolor, as my car is black, and I wanted it to blend in, even though it is never seen! ](*,)
The first step in the project, is removing your interior! You will be drilling, 8 holes, from underneath the car, into the space occupied by your seats. I also have an Anderson Ford Motorsport PMS system, underneath my passenger seat! Not taking any chances, here! Both seats, the rear bench, the sill plates, and shoulder belt bolts will need to be removed. This way, you can pull your carpeting, out of the way, for drilling. Here is my interior:
And my PMS system:
[img]http://img.photobucket.com/albums/1003/metalcop/89%20Stang%20GT/PMS1.jpg[/img]
Stay tuned, there is more to come!
Continuation of the install:
After the removal of the interior, you have to lift the car, to install the loop. I used jack stands, but an actual lift would have made the job much, much easier! If you use jackstands, remember to put them under the rear axle, to prevent it from hanging, and possibly interfering with the installation. Getting the loop in place isn't that difficult, as the two piece design allows for easy fitment. Actually, bolting the two pieces together, in place was probably the most difficult part of the installation! In this case, where the pieces are joined, the bolts will face up, towards the car, to provide maximum exhaust clearance, for your H-pipe. The NHRA regulation requires that the loop be installed within 6" of the front U-joint. I don't intend to drag race (not yet) but it makes sense to follow this regulation, the loop will have the most benefit, in this area. There is a nice flat spot, under the seat pans. Once I got the loop where I wanted it, I used this neat motorcycle lift, to hold it firmly in place, for drilling.
Then the tip is to drill a single hole, on one side, and mount the nut and bolt, snugly in place. Then go to the other side, and repeat with another single hole. This way, you can be sure that the loop will not shift, while you drill the remaining holes. I used the washers, in the only place necessary, where it actually made sense, on top of the interior sheet metal. I also placed the bolts, facing the ground, so that just the heads and washers are tucked under the carpet, providing minimal intrusion. The reason I mention this, is because there are other how-to's, on the net, and even on the 5.0 magazine website that show improper installation! I also used a good amount of silicone, so that it went under the washers and down the threads to completely seal up the holes. One of the other tips I picked up, is to only drill a 5/16" hole, which is the same size as the bolt. That way the bolt will actually thread through the hole, with no excess play or slop, from an oversized hole. I did have to chase a couple of the holes, with a tap, but most threaded, on their own. I didn't run into any issues, since I made sure of the proper alignment, by securing one bolt per side, first. Here is the installed pic from the top, drivers side:
Passenger side (you can see the rivet that holds the fuel lines in place, to the left of the bolt heads) :
From the bottom, drivers side, you can get a good view of the whole loop, here:
And the bottom, passenger side:
The fuel lines run very close to the passenger side, so make sure that the loop is forward where the lines are riveted to the p.s. floor pan. I also painted over the area, where the bolts come through, with textured undercoating paint, to hide the mod, and provide further sealing. BTW, that crappy off-road H-pipe, with its non-mandrel bends, is soon to be a thing of history. I have a Magnaflow, catted H-pipe, waiting to go on, soon.
http://www.youtube.com/watch?v=k9DVlnX0jIc
So I chose the Ford Racing loop, made by HPM. The products that Ford Racing puts their name on, in my experience, are well built and also fit very well. The FRRP loop is also specifically designed, to clear the FRRP oversized aluminum driveshaft, which I am running. Unfortunately, the part is now discontinued, and I had links to Jeg's and Steeda, to purchase it, that are now dead. Luckily, I found that Brothers Performance had 1 (!) left, so I ordered it up. Here is how it is 'supposed' to come:
Mine came with only 4 nuts/bolts to hold the loop brace to the cross brace, none of the bolts to mount the assembly to the car!? I called Brothers Perf. and they said that I got the last one, there was no way they could even verify that it was supposed to come with the other nuts/bolts/washers etc. Honestly, I was just looking for a partial refund, or maybe some in-store credit? Anyway, I got nothing, other than a "sorry, I guess you'll have to go to the hardware store." Oh well, previously I have had excellent experiences with Brothers, so really no big deal. I had always intended to replace the included hardware with grade 8 bolts/washers, anyway, but the 12 grade 8 - 5/16" bolts/washers and stop nuts cost me an extra $10. DS safety loop was $50 shipping included, BTW. For those who still need one, Summit sells an exact copy of the FRRP product, with the only difference being theirs is powdercoated black, the FRRP is zinc coated. I painted mine with self-etching primer and gloss black Duplicolor, as my car is black, and I wanted it to blend in, even though it is never seen! ](*,)
The first step in the project, is removing your interior! You will be drilling, 8 holes, from underneath the car, into the space occupied by your seats. I also have an Anderson Ford Motorsport PMS system, underneath my passenger seat! Not taking any chances, here! Both seats, the rear bench, the sill plates, and shoulder belt bolts will need to be removed. This way, you can pull your carpeting, out of the way, for drilling. Here is my interior:
And my PMS system:
[img]http://img.photobucket.com/albums/1003/metalcop/89%20Stang%20GT/PMS1.jpg[/img]
Stay tuned, there is more to come!
Continuation of the install:
After the removal of the interior, you have to lift the car, to install the loop. I used jack stands, but an actual lift would have made the job much, much easier! If you use jackstands, remember to put them under the rear axle, to prevent it from hanging, and possibly interfering with the installation. Getting the loop in place isn't that difficult, as the two piece design allows for easy fitment. Actually, bolting the two pieces together, in place was probably the most difficult part of the installation! In this case, where the pieces are joined, the bolts will face up, towards the car, to provide maximum exhaust clearance, for your H-pipe. The NHRA regulation requires that the loop be installed within 6" of the front U-joint. I don't intend to drag race (not yet) but it makes sense to follow this regulation, the loop will have the most benefit, in this area. There is a nice flat spot, under the seat pans. Once I got the loop where I wanted it, I used this neat motorcycle lift, to hold it firmly in place, for drilling.
Then the tip is to drill a single hole, on one side, and mount the nut and bolt, snugly in place. Then go to the other side, and repeat with another single hole. This way, you can be sure that the loop will not shift, while you drill the remaining holes. I used the washers, in the only place necessary, where it actually made sense, on top of the interior sheet metal. I also placed the bolts, facing the ground, so that just the heads and washers are tucked under the carpet, providing minimal intrusion. The reason I mention this, is because there are other how-to's, on the net, and even on the 5.0 magazine website that show improper installation! I also used a good amount of silicone, so that it went under the washers and down the threads to completely seal up the holes. One of the other tips I picked up, is to only drill a 5/16" hole, which is the same size as the bolt. That way the bolt will actually thread through the hole, with no excess play or slop, from an oversized hole. I did have to chase a couple of the holes, with a tap, but most threaded, on their own. I didn't run into any issues, since I made sure of the proper alignment, by securing one bolt per side, first. Here is the installed pic from the top, drivers side:
Passenger side (you can see the rivet that holds the fuel lines in place, to the left of the bolt heads) :
From the bottom, drivers side, you can get a good view of the whole loop, here:
And the bottom, passenger side:
The fuel lines run very close to the passenger side, so make sure that the loop is forward where the lines are riveted to the p.s. floor pan. I also painted over the area, where the bolts come through, with textured undercoating paint, to hide the mod, and provide further sealing. BTW, that crappy off-road H-pipe, with its non-mandrel bends, is soon to be a thing of history. I have a Magnaflow, catted H-pipe, waiting to go on, soon.
Labels:
1989 Mustang,
Brothers Performance,
driveshaft,
Flofit,
Ford Racing,
GT,
HPM,
loop,
safety,
Saleen,
seats
Subscribe to:
Posts (Atom)